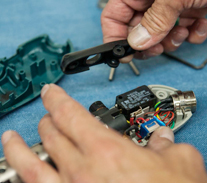
Like an automobile, torque tools require periodic servicing and calibration. When you purchase a tool for your manufacturing facility, it is an investment. You are accepting ownership of that equipment and are responsible to keep it operating in peak performance. Failure to properly maintain a torque tool leads to unnecessary expenses, potential product failures and production delays. Often, proper tool use and maintenance are ignored.
To maintain consistent performance and accuracy, torque tools must be checked regularly. Early detection of worn parts or when a tool starts to drift out of tolerance will reduce unwanted expenses. A power or hand tool is a measuring tool that must be properly calibrated and maintained. Regular maintenance and torque calibration ensures repeatable performance and accuracy, as well as adherence to international standards. Simply, prevent premature tool failures and avoid costly shutdowns.
When implementing torque equipment into your assembly process, it’s important to also create a maintenance schedule and budget for each tool. It’s better to be proactive than reactive. Make sure you know how to properly operate the equipment. Read the operating instructions. Ensure your staff is trained to properly operate the torque tool. Never assume all tools operate the same. Learn the requirements needed to maintain the equipment. Improper use and irregular maintenance are key ingredients for a tool failure. Create a plan of action within your organization that prevents these issues from incurring. With proper care, a quality torque tool will continue operate for many years with precision torque control.
Planning a maintenance schedule for a tool requires you to evaluate the fastening application as well as the frequency of use. Is the tool tightening a few fasteners a day or hundreds and hundreds a day? How are you calculating or monitoring the frequency a torque tool is being used? Ultimately, it is the organization that owns the tool that must determine a suitable maintenance and calibration frequency that best fits their needs. Maintenance plans should continually be reviewed and updated. The goal is to keep tools in safe, reliable, and operational condition.
When evaluating a torque tool for your assembly application, don’t overlook the required maintenance costs necessary to maintain it. Are you considering potential maintenance expenses down the road? As technology advances in the design of torque tools, some equipment are being built to reduce standard maintenance costs, like brushless electric screwdrivers. When comparing these tools with standard electric screwdrivers that use a brush motor design, you should consider the benefits offered with a brushless power tool. A brushless motor tool reduces the standard maintenance costs. Featuring wear-free components, like no brushes to wear out, the life cycle costs with brushless assembly tools are reduced.
Planning a maintenance budget is really dependent on the quality and types of torque tools being used. Developing a maintenance budget should be a result of analyzing historical data. Always keep maintenance records for all your tools. You can segment a budget into two categories. One is a yearly routine maintenance budget and the other being an emergency maintenance budget for unanticipated expenses. Also, review the tools at your facility that constantly require short-term maintenance cycles and rapidly deplete your maintenance budget. It may be time to invest in an alternative solution. A common tool that requires a lot of maintenance is an impact wrench.
Impact wrenches are a commonly used tool in the world. Often buyers are lured into purchasing an impact wrench because it is inexpensive. A low cost tool is often a short-term solution. An impact wrench is not ergonomically friendly to an operator and the tool requires a high maintenance budget. The wrench typically needs service multiple times each year. A pulse tool would be a great alternative solution.
How do you know when a tool starts to drift out of tolerance and is in need of calibration? Consider having a torque analyzer system in the production area to serve as a line checker. Have your assembly operators or the quality control staff test the tools daily or weekly to ensure the tools aren’t falling out of calibration. If a tool displays any symptoms, have it pulled from the assembly line.
To minimize any production downtime, a good maintenance plan should include having backup tools on-site. When a tool needs to be pulled from the production line for service, there are different factors that can delay its immediate return. Some of these items cannot always be controlled. Spare parts might not be readily available. The time that is needed to ship a tool to a service lab and have it returned requires time. A backlog of service orders may cause delays. It’s worth the investment to have backup tools ready for deployment.
Be selective when choosing a calibration and service lab. A facility needs to comply with quality standards. A lab that is ISO 9001 certified and ISO 17025 accredited is a good starting point. Mountz features an experienced calibration and repair staff. Our trained technicians can calibrate and repair most any tool. Mountz provides rapid service with quality that you can trust as we offer two state-of-the-art calibration lab and repair facilities that can calibrate up to 20,000 foot-pounds. All calibrations are performed using NIST-Traceable standards, and meet the requirements of ANSI/NCSL Z540. Mountz is an ISO 9001 certified and ISO 17025 accredited company. Making a safer world through accuracy and precision is the core purpose of Mountz, Inc.
Proper tool maintenance along with good practices in safety, care, and storage will increase the life expectancy of your torque equipment. If you have torque tools in need of service or calibration, contact the Mountz service staff, they are ready to assist you.